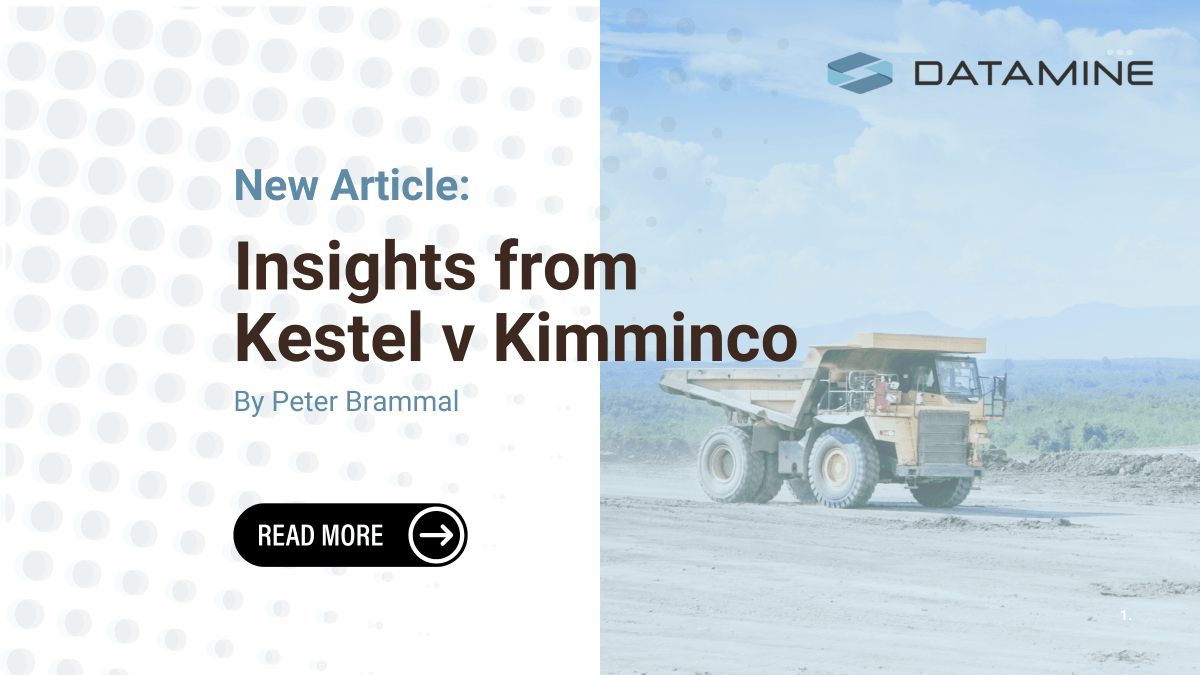
Customer Success Story:
Guinea Alumina Corporation & MineMarket
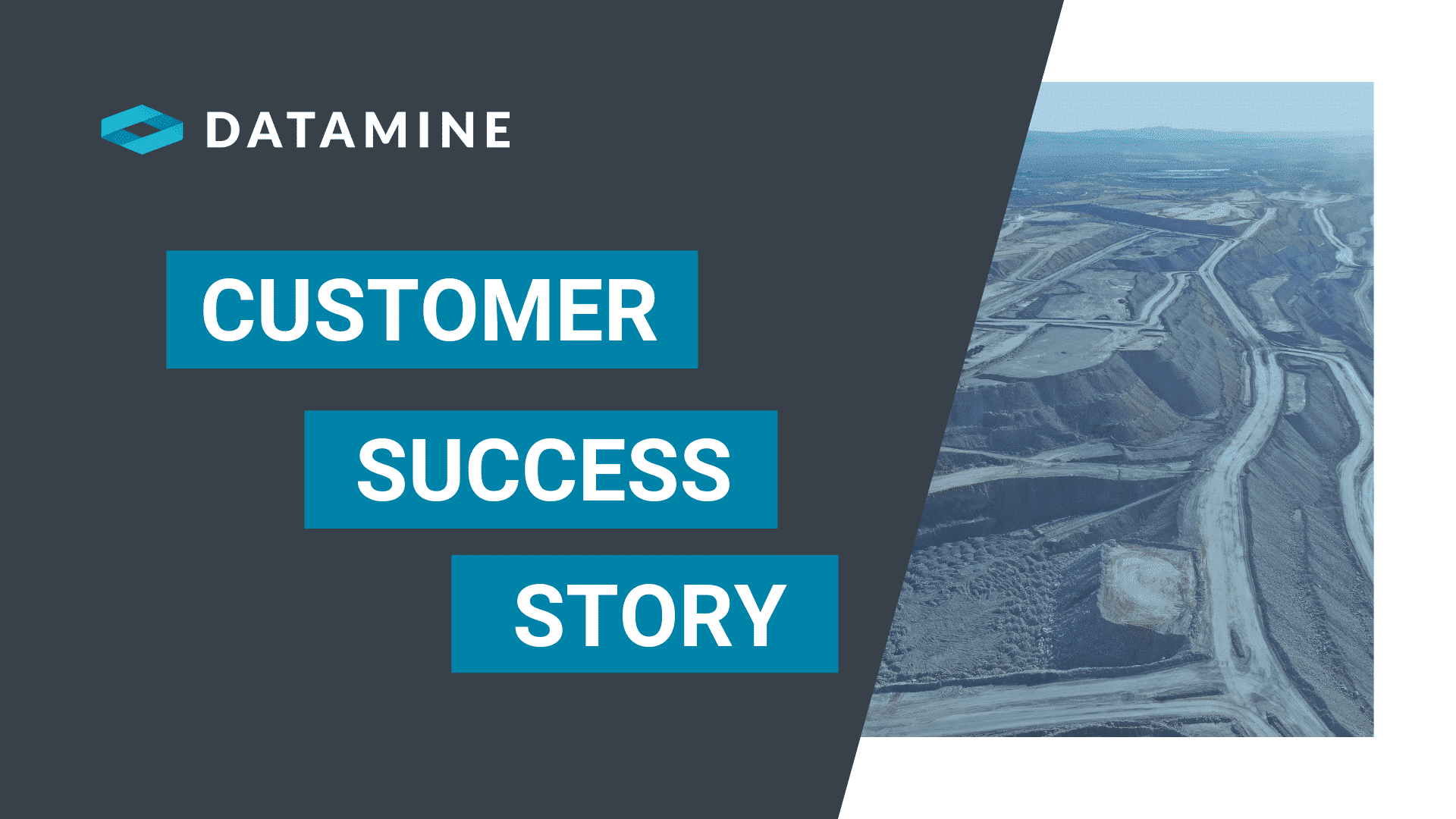
GAC Automated Their Systems and Transformed Their Operations with MineMarket, Saving Over 60 Man-Hours Every Day.
The customer
GAC have an exhaustive and crucial mine-to-market operation. Bauxite ore is exploited in the mine located closed to Sangaredi in the Boke province and railed for approximately 90km to the port facilities in Kamsar, on Guinea’s Atlantic coast. Car dumpers unload the bauxite ore, and a Stacker/Reclaimer operation loads material onto a barge loading conveyor belt. The barges navigate 37km into deeper waters where it is transhipped into Capesize vessels. The ore is then shipped by sea to customers in different locations all around the world. GAC’s facilities include some of the largest pieces of equipment ever installed in an African mining project.
The challenges
Data entry and validation took many hours every day for many employees across the entire business. Collecting, cleansing and entering data across the operation (mine, processing, railing, port and shipping) could take around 30 man-hours every day. Mine planners entered blocks into spreadsheets that would be emailed to mine contractors who would enter that same data manually into another system. Mining movements for every shift were recorded in spreadsheets before being consolidated into a daily movement report. Of course, at every stage, time would also be spent validating and reconciling the data.
The solution
MineMarket delivers increased supply chain visibility, enforces standardised business processes, improves control of production, supports complex commercial planning and operations, and enables regulatory compliance.
The results
Datamine’s willingness to enhance and improve the software to support industry 4.0 (i4.0) interoperability interface requirements was critical in moving to the next phase.
GAC’s second phase implementation of MineMarket went live from pit to port in November of 2021. This implementation takes advantage of full i4.0 integration, with automated data capture, calculations and publishing of stockpile states. With this automation, GAC can send more granular data to MineMarket, enabling real-time visibility of their inventory from blocks, through ROMS, post-crushing stocks, railing, port and shipping. Grade information is also available in real time as each sample analysis result is received.
Heinrich Armand Greyling, GAC IMS Project Manager, summarises the results, ‘Apart from fixing data source issues, … the system is completely automated, which saves effort and provides stockpile balance and grade information on average 15 hours earlier than [the] previous manual process.’
GAC are currently retraining employees and redeploying the time previously spent on manual tasks. Importantly, they are utilising this time to gain insights for business improvement initiatives. Operationally, they have greater control of grades throughout the value chain and have been able to seize opportunities to load barges directly from trains instead of rehandling stock at the port.
This was a challenging project on multiple fronts including i4.0 interface development and testing, COVID-19 impacts restricting site travel and engagement, changes in GAC’s teams and the workforce over the project duration, and the transition from ABB to Datamine. However, Heinrich explains that ‘The Datamine MineMarket team have accommodated to our challenges very well with all things considered. The team has been really good to work with.’
With MineMarket, GAC are now in a great position to integrate future extensions to their i4.0 architecture.
Company
- Guinea Alumina Corporation (GAC)
Industry
- Mining
Region
- Africa
Software Solution
- MineMarket
Challenges
- GAC had no systematic data management, with data manually collected and entered into spreadsheets​
- Data entry and validation was completed by many employee across the entire business and took many hours every day​
- There was an abundance of time spent collecting, cleansing and entering data across the operation (mine, processing, railing, port and shipping), manually entering blocks into spreadsheets & into different systems, and time spent validating and reconciling data
Outcomes
-
MineMarket replaced disparate spreadsheets and systems
-
Granular and consolidated data now available for improved real-time decision making
-
Automated data entry utilising industry 4.0 architecture
-
Up to 30 man-hours of manual data entry every day eliminated
-
Data entry for blocks that was a full-time job replaced with 1 hour per day for reconciliation and review
-
Daily stock movement reports automated
-
Saved time now being spent on business improvement initiatives
-
Reduced off-spec incidents and stock rehandling at port
Social Media
See our blogs
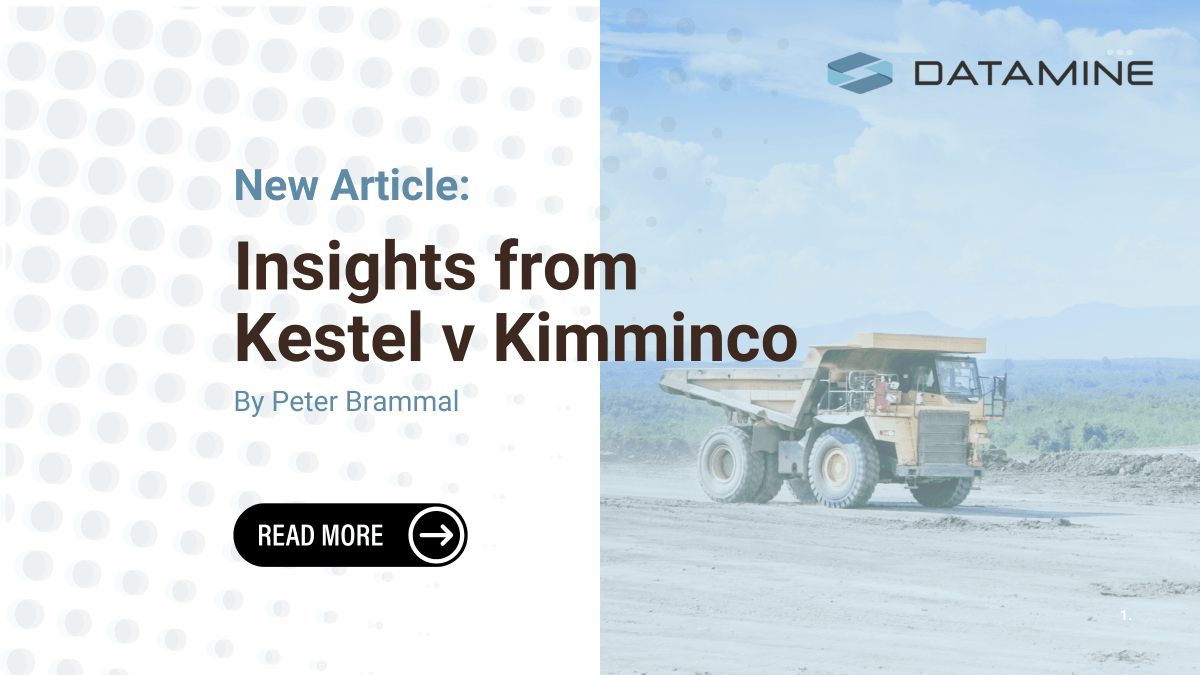
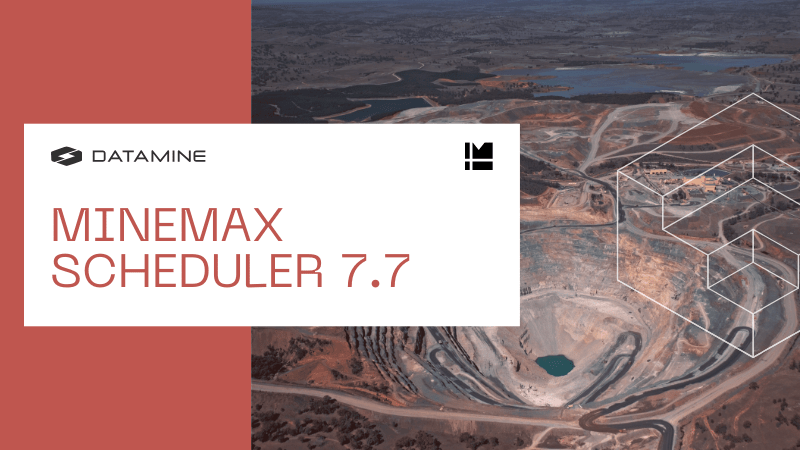
Minemax Scheduler 7.7
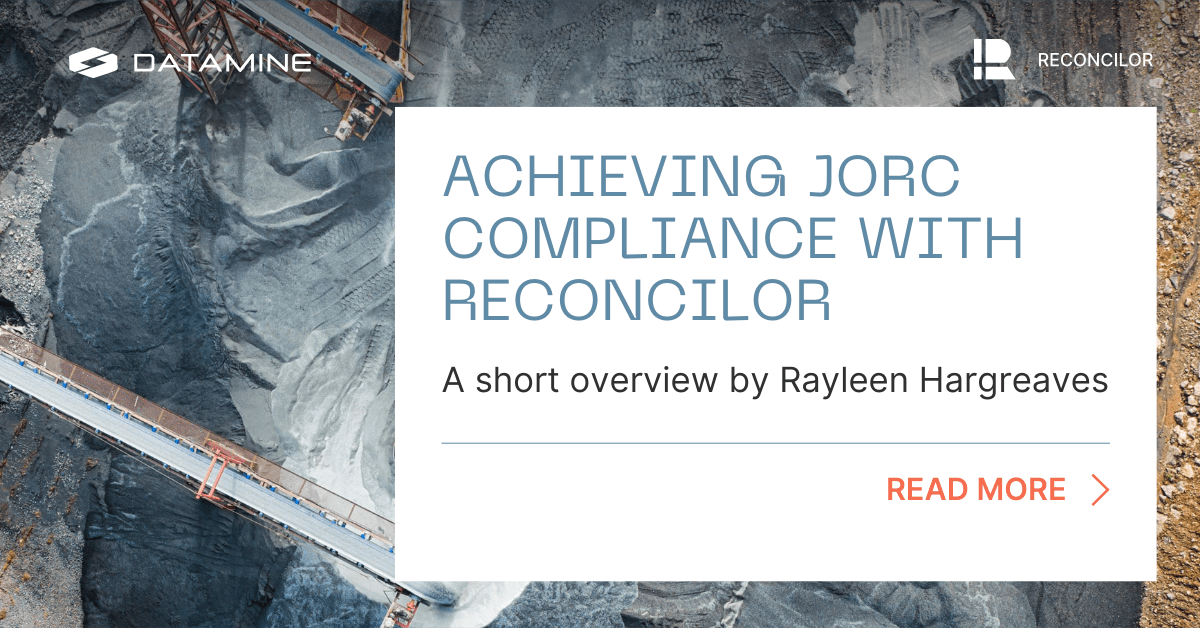
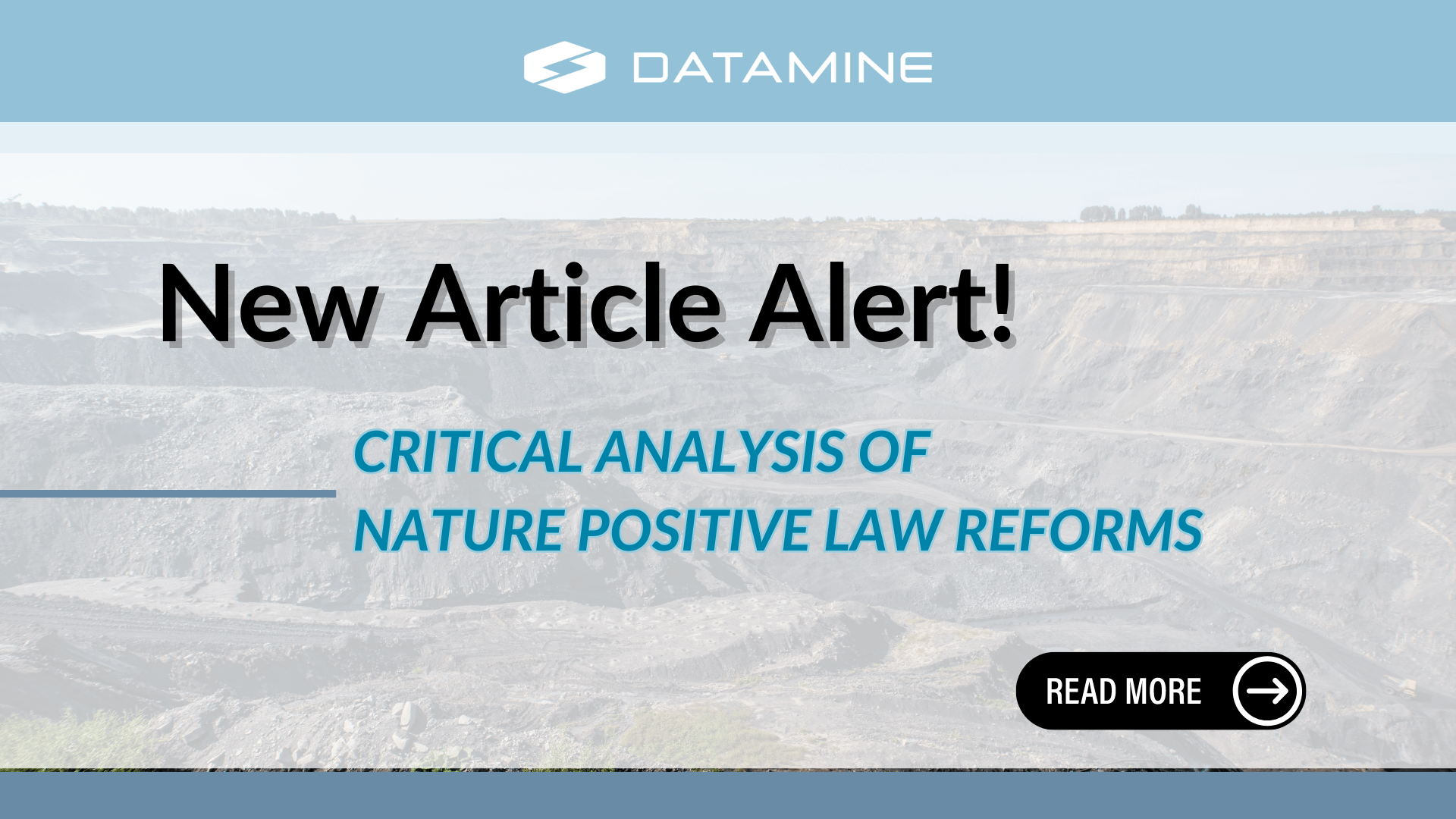
Critical Analysis of Nature Positive Law Reforms
-
Peabody & Datamine Consulting
Peabody Identified Gaps Within Their Operations And Improved Their Overall Technical Capacity With Datamine's Consultants
-
Rio Tinto & CCLAS
Automated Processes And Tracked Data Flows Enabled Rio Tinto To Improve Operational Outcomes - Saving Up To 1 Month Per Year In Manual Work, Significantly Minimising Data Errors And Increasing Processing Capacity
-
Advaita Group DMCC & MineMarket CTRM
Better Informed Decision Making And Data Analysis, And Significant Time Savings On EOM Reporting Using MineMarket​
